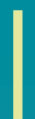 |
 |
Filling at ordinary Temperature → Boiling → Cooling → Dehydrating → Collecting & Packaging
Before, the product is hot-packed, kept warm and then cooled down. It is now filled at ordinary temperature, boiled and cooled down. With a kind of such cooking function, it is now being applied to wider variety of products.
|
|
|
Komack proposes the line that focuses on the traceability of the production process with the “Line Monitoring System” adopted.
1. |
Monitor the packaging conditions and filling temperature of the packaging machine, and the heating & cooling temperature and the processing time in the WAVE PASS tank to improve the product safety. |
2. |
Transfer the monitoring data to the PC and store the data in real time. |
3. |
Enable the products not suitable for the hot-pack to be cooked in the pack after packaged by extending the distances in the heat-retention (heating) tank. |
|
|
Komack System Uniline
This system is the “packet pasteurization line” which is consist of the heat exchanger, packaging machine, WAVE PASS (consecutive heat-retention, cooling, dehydration apparatus) and various collection systems.
|
|
Existing Features of the System
1. |
Keep the product warm and cool it down while kneading it so that the heat is exchanged evenly and effectively. |
2. |
Consecutively process the strip-shaped product so that the appearance of the product is not damaged. |
3. |
With pasteurization, does not deteriorate the color, flavor and aroma. |
4. |
Perform the complex process of heat-retention, cooling and dehydration consistently. |
5. |
Contribute significantly to the laborsaving in a series of work with the various collection systems connected in the post-process. |
|
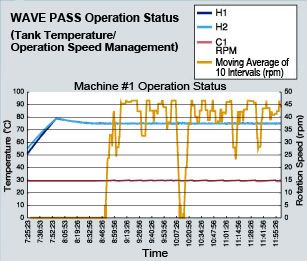 |
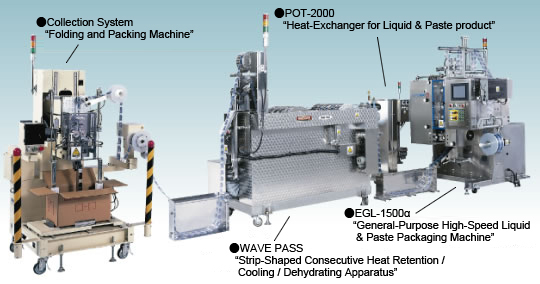 |
|
Variation of Optional Post Process
The additional post processing line can improve the efficiency in production and lead to the laborsaving.
|
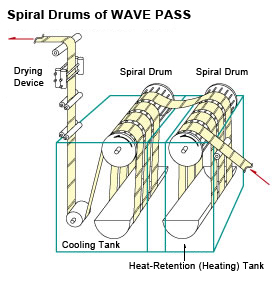 |
 |
 |
 |
Automatic Folding & Box Packing Machine for Strip-Shaped product |
Cut into a single pack + Bag-Feeding Automatic Bagging Machine |
Cut into a single pack + Automatic Box Packing Machine |
|
WAVE PASS Series
[Standard Specifications]
Model *1 |
Tank Capacity (L) *2 |
Tank Work Length |
Connected Pipe |
Power Consumption |
Machine Dimensions (mm) *4
Length (L) × Width (W) × Height (H)
|
Bag Width (mm) |
Heating |
Cooling |
Cooling System |
S-C1 |
200 |
|
|
7Lines/10 |
5Lines/7 |
4Lines/5 |
|
Feed |
15 |
9.9m/min. or less |
2.1 |
1170×1000×1850 |
Drain |
20 |
10m/min. or more |
3.6 |
M-C1 |
415 |
|
|
10Lines/18 |
7Lines/12 |
6Lines/10 |
|
Feed |
20 |
9.9m/min. or less |
2.1 |
1560×1200×2000 |
Drain |
40 |
10m/min. or more |
3.6 |
L-C1 |
730 |
|
|
14Lines/30 |
10Lines/20 |
8Lines/16 |
|
Feed |
20 |
9.9m/min. or less |
2.1 |
1560×1500×2220 |
Drain |
40 |
10m/min. or more |
3.6 |
L-C2 |
730×2 |
|
|
14Lines/30×2 |
10Lines/20×2 |
8Lines/16×2 |
|
Feed |
20 |
9.9m/min. or less |
2.1 |
2290×1500×2220 |
Drain |
40 |
10m/min. or more |
3.6 |
L-C3 |
730×3 |
|
|
14Lines/30×3 |
10Lines/20×3 |
8Lines/16×3 |
|
Feed |
20 |
9.9m/min. or less |
2.1 |
2940×1500×2220 |
Drain |
40 |
10m/min. or more |
3.6 |
Heating/ Cooling System |
S-H1C1 |
230×2 |
|
7Lines/10 |
5Lines/7 |
4Lines/5 |
|
7Lines/10 |
5Lines/7 |
4Lines/5 |
|
|
|
9.9m/min. or less |
2.1 |
1650×1000×1850
|
10m/min. or more |
3.6 |
M-H1C1 |
415×2 |
|
10Lines/18 |
7Lines/12 |
6Lines/10 |
|
10Lines/18 |
7Lines/12 |
6Lines/10 |
|
|
|
9.9m/min. or less |
2.1 |
2290×1200×2000 |
10m/min. or more |
3.6 |
L-H1C1 |
730×2 |
|
147Lines/30 |
10Lines/20 |
8Lines/16 |
|
147Lines/30 |
10Lines/20 |
8Lines/16 |
|
|
|
9.9m/min. or less |
2.1 |
2290×1500×2220 |
10m/min. or more |
3.6 |
L-H2C1 |
730×3 |
|
14Lines/30×2 |
10Lines/20×2 |
14Lines/16×2 |
|
14Lines/30 |
10Lines/20 |
14Lines/16 |
|
|
|
9.9m/min. or less |
2.1 |
2940×1500×2220 |
10m/min. or more |
3.6 |
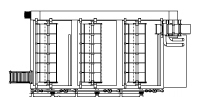 |
[Digital heat regulator is employed for the temperature control]
* 1. Right (R) of left (L) for the work inlet can be selected on each type.
* 2. Tank capacity of the L-size may vary by the interior width of the tank.
* 3. The work length in the tank may vary by the number of lines.
* 4. For L-size, the interior width of the tank is selectable in the range of 800mm-1200mm.
* 5. Steam pressure of the heating tank should be set to 0.3Mpa or less.
|
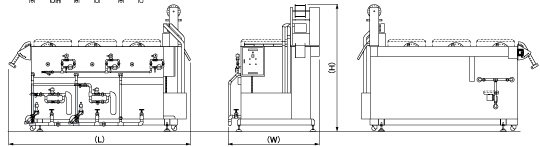 |
POT-800/2000/3000 Pot Series
The POT Series can be used widely as a heat exchanger for liquid/paste materials.
For the hot pack, it is required to ensure the stable filling temperature to prevent uneven filling volume, and the heating time (holding time) for the pasteurization.
The POT series is easy-to-maintain, equipped with the sanitary piping using SUS316 for the wetted part, and the heat-detention tank and the corrugated tube that can be detached and washed separately. The corrugated tube is replaceable, and available for purchase for overhaul.
[ Standard Features ]
|
POT-800 |
POT-2000 |
POT-3000 |
Heat Exchange |
6,400kcal/h |
21,000kcal/h |
31,600kcal/h |
Corrugated Tube Size |
10A×8m |
15A×20m |
15A×30m |
Heat Transfer Area |
0.34㎡ |
1.12㎡ |
1.67㎡ |
Steam Pressure |
Up to 0.2MPa |
Up to 0.2MPa |
Up to 0.3MPa |
Retained Water Volume |
16L |
55L |
142L |
Feed Pipe |
15A |
15A |
15A |
Drain Pipe |
15A |
20A |
20A |
Steam Pipe |
15A |
15A |
20A |
Product Inlet/Outlet |
1S Ferrule |
1S Ferrule |
1S Ferrule |
Material of Corrugated Tube |
SUS316L |
SUS316L |
SUS316L |
Material of Tank |
SUS304 |
SUS304 |
SUS304 |
Material of Main Unit |
SUS304 |
SUS304 |
SUS304 |
Residual Liquid |
1.4L |
4.9L |
7.4L |
Power Consumption |
AC 100V 80W |
AC 100V 80W |
AC 100V 80W |
Dimensions of Machine |
W650mm D360mm H1,200mm |
W800mm D400mm H1,500mm |
W800mm D500mm H1,650mm |
Operating Weight |
71kg |
130kg |
228kg |
Weight of Machine |
55kg |
75kg |
86kg |
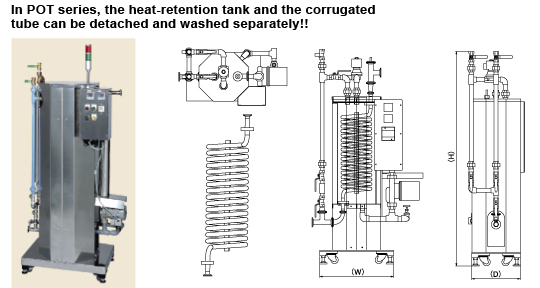 |